How to Understand Warehouse Terminology
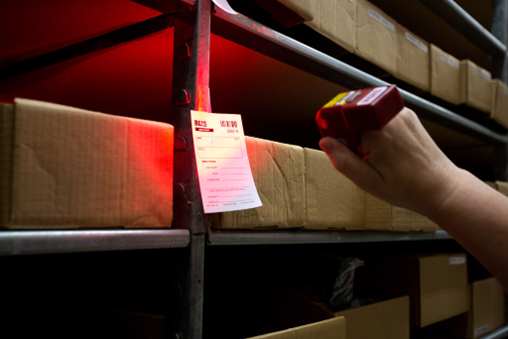
Let’s be honest – the world of warehousing can seem a bit of a jargon-fest. From ‘slotting’ to ‘RTVs’, it’s easy to get lost in the terminology. But understanding these core terms isn’t just about impressing your colleagues; it’s about improving efficiency, streamlining operations, and ultimately, boosting your bottom line. Here’s a breakdown of the most common warehouse terminology and their meanings..
Building a Solid Foundation: Essential Warehouse Terminology
This list covers everything from inventory management to shipping logistics – understanding these terms will make anybody’s job within the warehouse industry easier.
- 3PL (Third Party Logistics): This simply means using a warehouse or group of warehouses managed on your behalf – letting specialists handle your stock.
- 4PL (Fourth Party Logistics): Think of a 4PL as a single interface – managing relationships with multiple logistics service providers on your behalf.
- Active Stock: Stock in the picking locations ready for order fulfillment – the stock actually available to ship.
- Aisle: Any passageway within a storage area – essential for movement and access.
- ATA (Actual Time of Arrival): The real time a shipment arrives, not just the scheduled arrival.
- ATD (Actual Time of Departure): The actual time a shipment leaves the warehouse.
- Backorder: A piece of stock ordered but out of stock, with a promise to ship once it’s available – managing customer expectations is key here.
- Bar Coding: A way of encoding data using barcodes – offering fast and accurate readability – crucial for picking and inventory.
- Blind Receiving: Receiving goods without a Purchase Order or invoice – a potential headache that requires careful processes.
- Buffer Stock: Keeping extra stock to protect against unexpected surges in demand or shortages.
- Cage: Used for security and to transport stock between locations.
- Cargo: Merchandise being transported by a vehicle.
- Compliance: Ensuring all products, processes, and documentation meet specific regulations.
- Consolidation: Combining shipments from multiple suppliers into one.
- CDOT (Complete and On Time Delivery): Measuring delivery performance – a key performance indicator (KPI).
- Course: A single layer of units making up a unit load (e.g., a pallet).
- Cross Aisle: A passageway at right angles to main aisles, for movement of supplies and staff.
- Cross Docking: Goods received at the warehouse are immediately shipped, rather than stored.
- Cycle Count: A systematic count of a portion of the stock, done regularly for accuracy.
- DC (Distribution Centre): The same as a warehouse – a central location for storing and distributing goods.
- DDP (Delivered Duty Paid): The seller is responsible for all import duties and taxes.
- DDU (Delivered Duty Unpaid): The buyer is responsible for all import duties and taxes.
- DSD (Direct Store Delivery): Goods delivered directly to a retail store.
- EAN (European Article Number): The European equivalent of the UPC.
- FIFO (First In First Out): The stock is shipped based on when it was received.
- Fixed Slot: A dedicated slot for a specific product.
- Floating Slot: A slot available for any product when empty.
- Fulfillment: The entire process of fulfilling a customer order – from picking to shipping.
- GTIN (Global Tracking Item Number): A unique product identifier.
- Landed Cost: The total cost of a product, including shipping, duties, and taxes.
- Merge in Transit: Combining shipments from multiple suppliers.
- Order Picker: A warehouse worker who picks orders from picking locations.
- Pallet: A flat platform for storing goods, typically used with a forklift.
- Pallet Picking: Retrieving entire pallets of goods.
- Perpetual Stocktaking: Tracking every transaction (in and out) to maintain accurate records.
- Physical Stocktaking: A complete inventory count of all stock.
- Picking: Selecting the items needed to fulfil an order.
- Pick List: A list of items to be picked.
- POD (Proof Of Delivery): Confirmation that the order was successfully delivered.
- RFID (Radio Frequency Identification): Using radio waves to track items.
- RTV (Return To Vendor): Sending returned goods back to the supplier.
- Shrinkage: Losses due to theft, damage, or errors.
- SKU (Stock Keeping Unit): A unique product identifier.
- Slotting: The placement of products within a warehouse.
- Sortation: Separating items for different destinations.
- SSCC (Serial Shipping Container Code): A unique code for shipping containers.
- UPC (Universal Product Code): The standard barcode.
- WMS (Warehouse Management System): Software to manage warehouse operations.
- Zone Picking: Dividing a picking list by zones.
Understanding these terms isn’t just about ticking a box; it’s about building a more efficient and effective operation.