Why the Supply Chain Matters
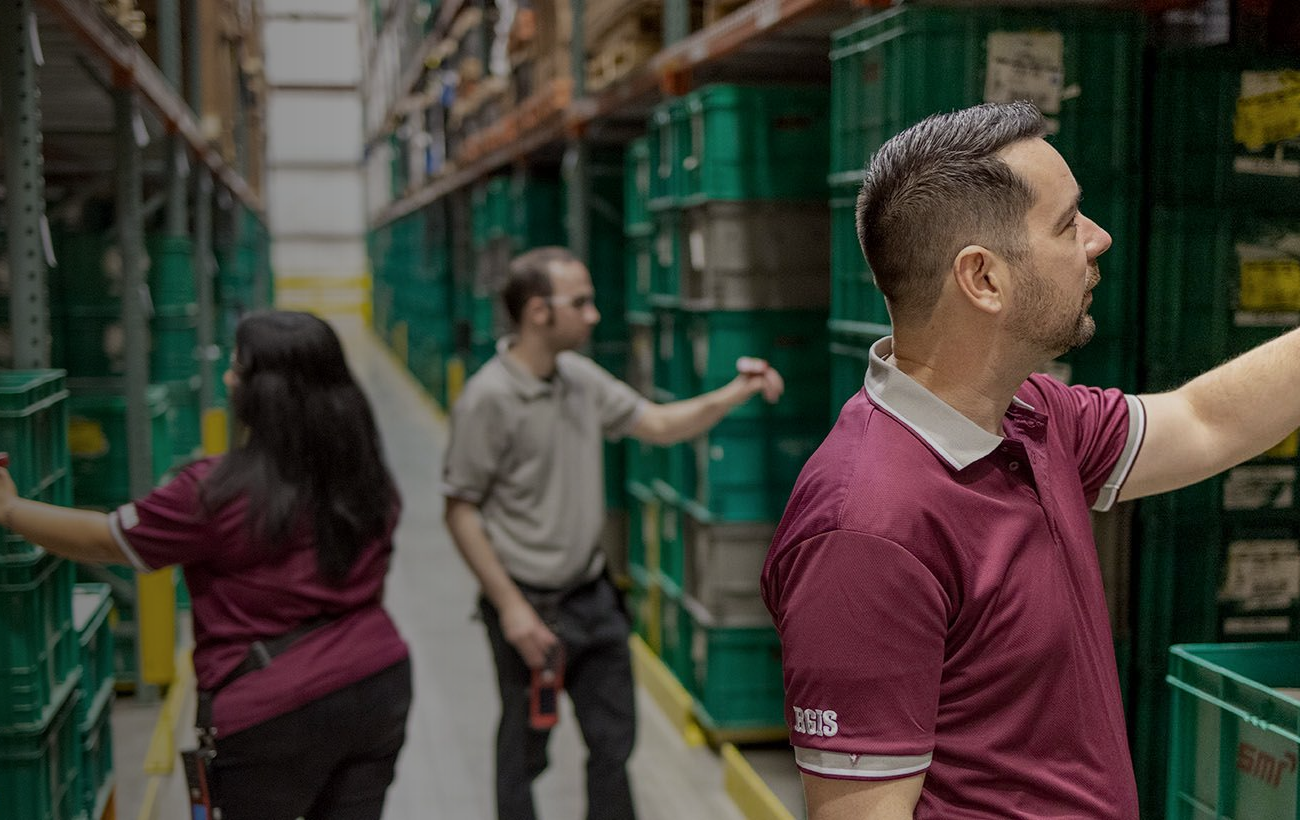
Understanding the importance of a supply chain can be illustrated by an unlikely example — the infamous Oscars blunder. The wrong envelope was handed over, leading to the wrong film being announced as Best Picture. “La La Land” was declared the winner when it was actually “Moonlight”. It was a moment of chaos, confusion, and embarrassment — all due to a breakdown in process. In many ways, that’s exactly what happens when the supply chain fails.
It’s also important to understand the distinction between the supply chain and logistics.
What is a Supply Chain?
A supply chain is a network of people, organisations, activities and data that work together to move a product or service from the supplier to the customer.
A simple supply chain can be broken down into five core stages:
-
Supplier (providing raw materials)
-
Manufacturer
-
Wholesaler
-
Retailer
-
Customer
What is Logistics?
Logistics refers to the coordination of activities required to move goods through the supply chain. It’s about ensuring the right product reaches the right customer, in the right quantity, in the right condition, at the right place, at the right time, and at the right cost — commonly known as the Seven Rs of Logistics.
While logistics focuses on the operations, the supply chain is the broader system of organisations working together to ensure products or services are delivered efficiently and accurately.
Key Elements of an Effective Supply Chain
To run a successful supply chain, the following areas must be tightly managed:
-
Stock – Whether you’re supplying raw materials or selling finished goods, it’s vital to know exactly what stock you have and where it is. Inventory accuracy is essential.
-
Data – Seamless information sharing across the supply chain increases efficiency. When every link in the chain has access to the same real-time data, it reduces errors and cuts down on waste.
-
Delivery – Commitments must be met. If you’ve promised to deliver to a customer or the next point in the chain, it’s critical that the goods arrive on time and in good condition.
-
Finances – Transportation, labour, warehousing and distribution costs all add up. If these aren’t monitored, it can negatively impact the performance of the entire supply chain.
The Payoff
A well-managed supply chain improves customer satisfaction by ensuring products are delivered accurately and on time. It also helps reduce waste, streamline operations, and improve profit margins.
Failing to manage the supply chain effectively — giving the wrong product to the wrong person — can result in unhappy customers, lost revenue, and embarrassing mistakes. Just ask the team behind that Oscars envelope mix-up.
Quote referenced from “Supply Chain Management: A Logistics Perspective” by John J Coyle et al.