Improving Order Picking Accuracy in Your Warehouse
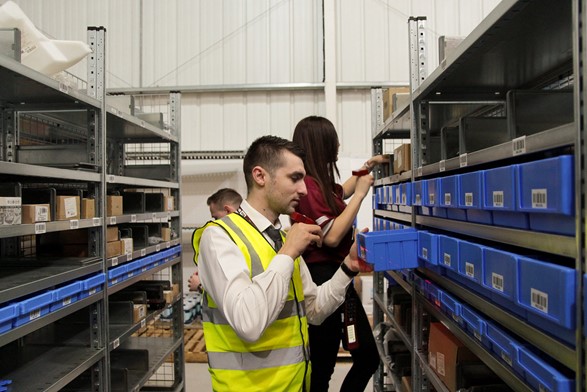
In any business, there are tight timeframes in which products must be processed and dispatched to customers. If an order arrives late or contains the wrong item, it may prompt the customer to look elsewhere the next time they need something.
Maximising order picking accuracy is essential to ensure the correct product reaches the right customer within the expected timeframe.
To improve accuracy, consider the following best practices:
-
Ensure all packing and picking processes are clearly documented. Procedures must be consistent, error-free, and strictly followed by warehouse staff.
-
Do not mix multiple SKUs (Stock Keeping Units) in the same location. If pickers are forced to search through different SKUs, it wastes valuable time. Assign a dedicated pick location for each SKU.
-
Maintain regular communication with warehouse staff. This helps to quickly identify any issues or errors, understand why they occurred, and implement measures to prevent recurrence.
-
Display individual and team error rates or accuracy levels. Recognising high performers can motivate staff and highlight potential mentors for colleagues who may need additional support.
-
Double or triple-check all paperwork for items entering or leaving the warehouse. Attention to detail at this stage helps to avoid costly mistakes.
-
Ensure 100% product availability with a reliable stock control system. This prevents pickers from wasting time searching for out-of-stock items.
-
Manage SKU locations carefully. High-demand products should be positioned at easily accessible locations, ideally at ground level, to speed up the picking process.
Conclusion
Pick accuracy is a critical aspect of operational efficiency. By implementing the above guidelines, businesses can improve fulfilment accuracy and ensure timely deliveries. When customers consistently receive the right products on time, they are more likely to return and recommend the service to others.