Aerospace Spare Parts Inventory Count
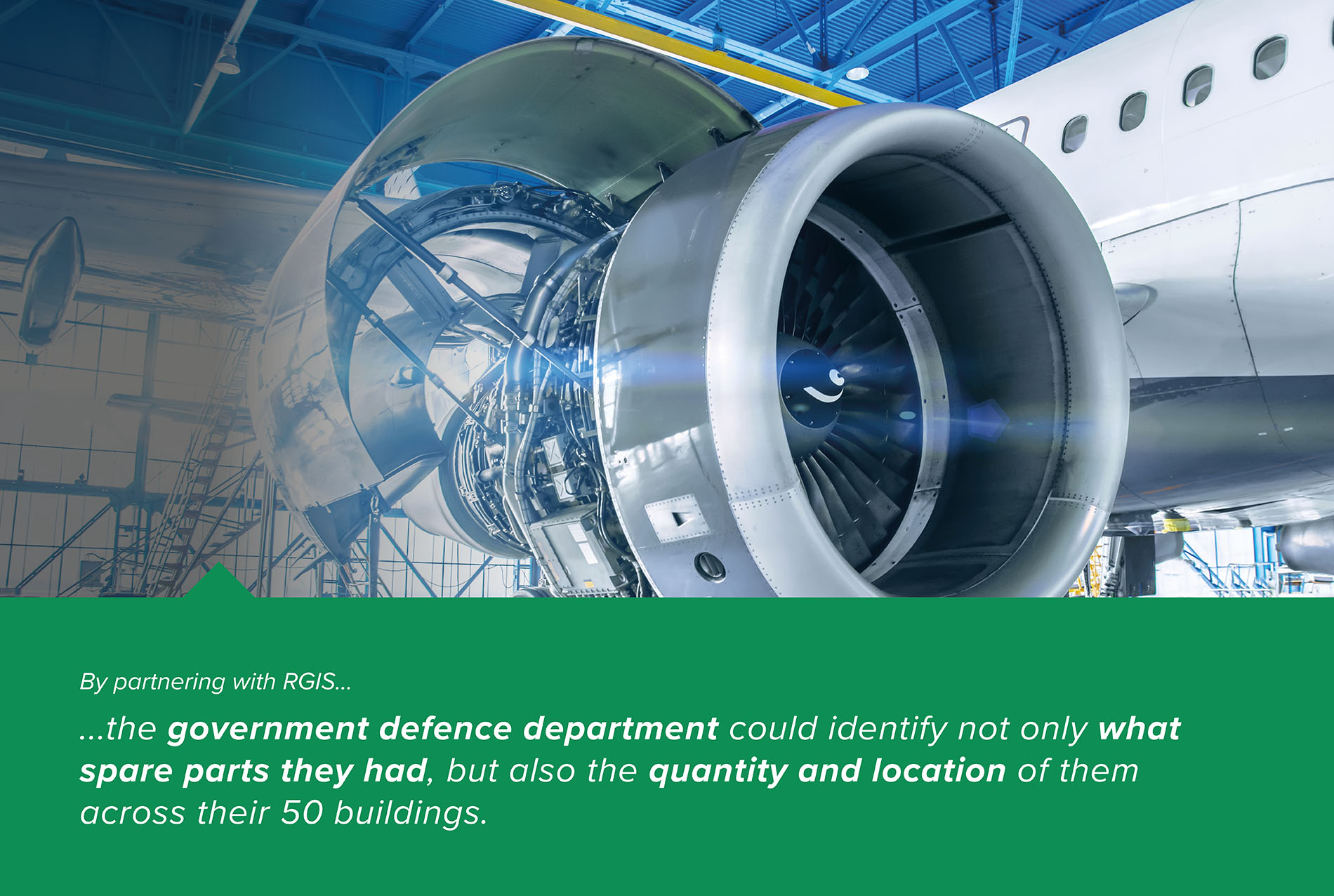
Our customer works for the government defence department providing the complete supply chain of a variety of defence vehicles including aircraft for military defence and their spare parts. Within the supply depot RGIS were asked to count the spare parts that were spread over 50 buildings in a variety of shapes and sizes.
REQUIREMENT
The defence company partnered with RGIS to achieve a full wall-to-wall stocktake of every line item. Also then produce and re-label each product so it could be clearly identified.
One of the difficulties the customer had was that the exact number of line items was unknown. This was due to data migration issues when the government body moved to a newer stock management system. The requirements were as follows:
- Preparation was paramount as there was a need to work alongside their facilities management company
- A plan was drawn up that allowed the facilities management company to efficiently clean the racking and products. Prior to RGIS completing the stocktake
- The stock count consisted of spare parts that were spread over 50 buildings in a variety of shapes and sizes
- Due to the highly sensitive nature of the parts, the RGIS teams were required to count and provide the information back within a strict time frame
- It was important to have all the data formatted correctly. So that it could be efficiently fed back into the supply chain management system
SOLUTION
RGIS worked on providing a wall-to-wall stock count of the 50 buildings:
- RGIS deployed a team of 14 trained staff fully housed within the client’s secure compound
- It was anticipated that the stocktake would last 12 months with a contingency for a further 6 months should it be deemed necessary
- It was anticipated that the number of line items would exceed 100,000 in total. With many of these items found in the various 50 buildings
- The pre-stocktake planning was critical in reducing downtime and allowing the data to flow daily to the customer. So it could be checked prior to uploading onto the system
RESULTS
The defence company found partnering with RGIS meant that the time, effort and cost of an internal resource to count was significantly reduced:
- The customer was able to identify the exact number of stock items. Which they had not been able to do since the move to a newer stock management system
- It meant the customer could identify where each of the stock items was located
- The government defence department could ensure that they were not over ordering parts. Which they already had in stock in another location