Efficient and Accurate Product Code Inventory of Warehouse using RGIS Vision
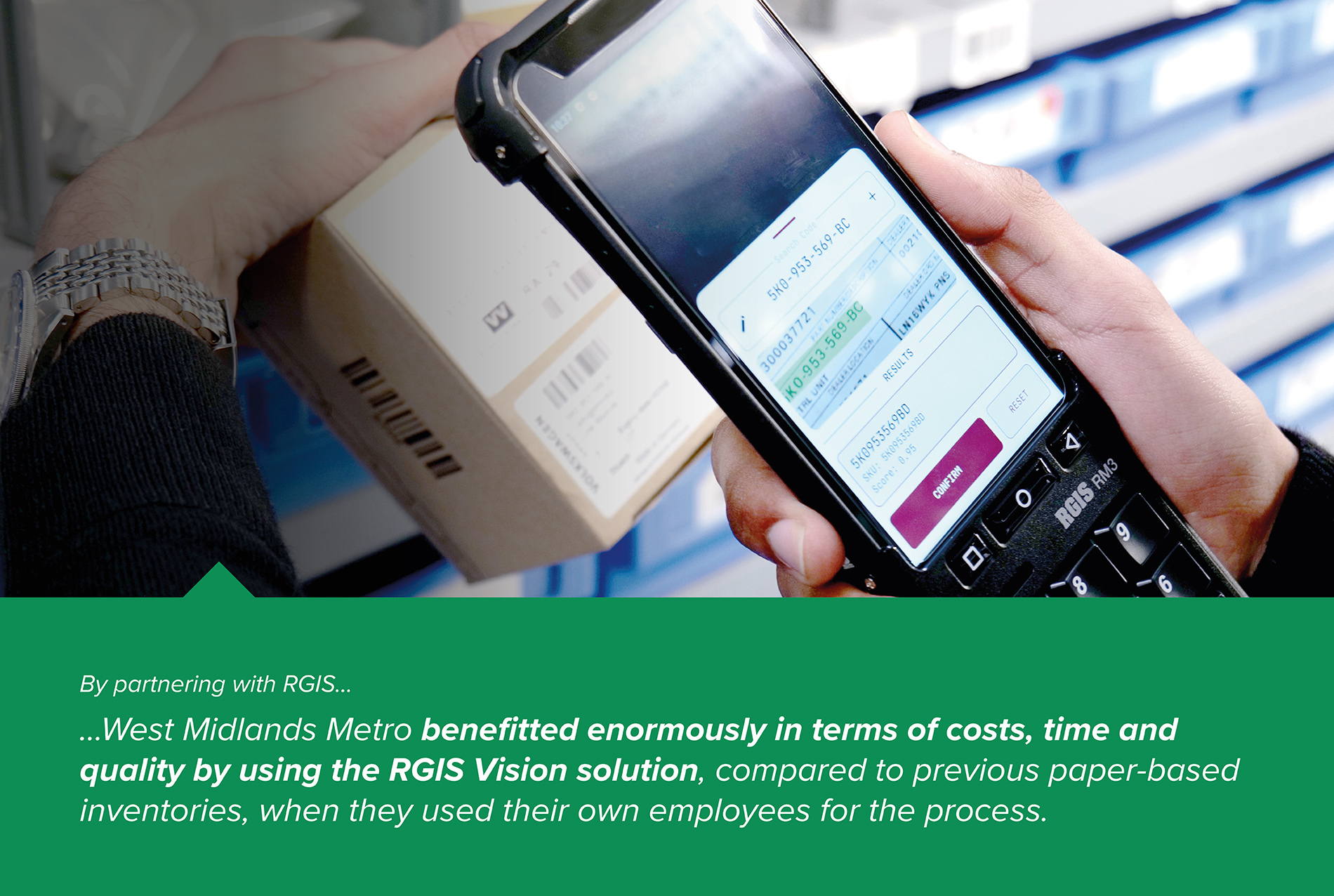
West Midlands Metro is a light-rail/tram operator in the county of West Midlands, England. With over 20 trams and more than 23km of track to look after and repair, the warehouse in Birmingham is a very busy depot.
REQUIREMENT
West Midlands Metro could not supply adequate internal employee resources for their annual product code inventory count. Having previously completed stocktakes in-house using the pen and paper process, they also found it to be very time-consuming, so they approached RGIS to provide the following:
- Complete an inventory count of all stock in the warehouse with product codes
- Identify variances to expected stock levels
- Provide accurate variance reports
SOLUTION
West Midlands Metro partnered with RGIS to complete the warehouse product code inventory project using RGIS Vision, and provided the following:
- Scheduled an experienced team of five RGIS Auditors and an Area Manager for the duration of the project
- As the customer had previously just used a paper-based stocktake process, RGIS introduced them to our revolutionary new scanning tool, RGIS Vision
- RGIS teams set up tests to scan the part codes with the powerful camera and worked with their stock file to create a simple checking process for any variance
- As the customer’s bin locations had challenging names, the RGIS solution was to use a variance report based on the RGIS ranges used. Ranges were matched to the bin locations, so the customer could still reference any products in the incorrect location
RESULTS
West Midlands Metro found by outsourcing the warehouse product code inventory project to RGIS, the following results were achieved:
- Accurately counted over 45,000 stock items and just under 2,000 SKUs
- RGIS Vision reports provided the customer with results that showed an accurate variance, which was a huge time saver for them
- Our accurate part code recognition software, RGIS Vision, allowed us to verify as we progressed, and then return a file with every line that showed no variance back to the customer
- From the final output, the customer only had 300 lines that required a manual change on the system, which was another massive time saver for them
- The customer found the whole process of moving away from internal staff to a professional company, improved accuracy on the first counts, and efficiency in completing the count within the agreed time frame
- The benefits of using RGIS Vision were very evident to the customer as we could track variances as we progressed, which in turn vastly reduced their data input time post-count
- Based on the positive outcome of the RGIS Vision warehouse inventory project, the customer has awarded RGIS the contract for the following year
TESTIMONIAL
“We had previously used a manual pen and paper process, and this involved using internal staffing such as drivers, and engineers. We wanted to move away from this and contacted RGIS. They showed us their cloud-based program that used a camera on their handsets to capture the part codes and created an excel stock file. This was a massive time saver when we had finished to enter the count data back into our system as they were able to check variances as they progressed and when we finished, we had very little left to adjust on our system. Overall, this has been a huge improvement on our previous process and we will be using RGIS next year.”
Kyle, West Midlands Metro