Identifying Missing Products Within a Third Party Logistics Warehouse
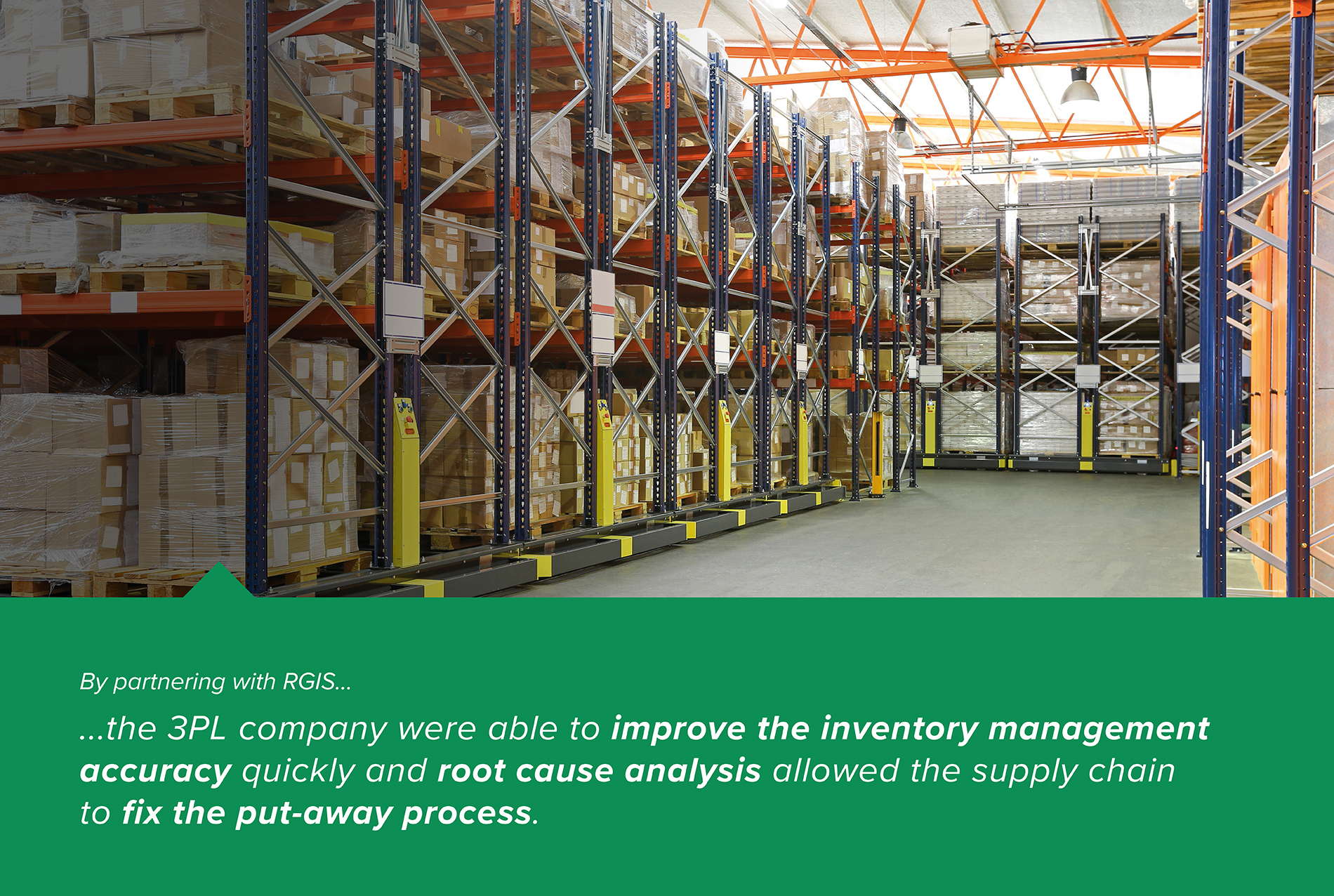
A 3PL company that offers warehousing, co-packaging, and transportation services required the support of RGIS. The company work to provide seamless logistics services for their customers. The warehousing and distribution services decrease costs for customers, increase efficiency, and improve the overall performance of the integrated warehousing solutions.
REQUIREMENTS
The 3PL company needed a solution to locate missing products. Parts were being put away in incorrect locations resulting in lost products, which then resulted in picking errors and incorrect on-hand counts in expected locations.
The 3PL company required RGIS to provide the following:
- Support for a 10-month project
- The project involved locating missing parts
- During the project, the warehouse needed to stay operational 24/7
- It was imperative that lost parts be found and reprocessed immediately
SOLUTION
The third party logistics company partnered with RGIS to complete the 3PL lost products project, and RGIS provided the following:
- Dedicated teams of seven experienced RGIS auditors per shift
- Two to three shifts per day during the 10-month project
- During the project, missing parts were constantly being located, flagged, and reprocessed
- Data was collected that allowed the supply chain provider to perform root cause analysis
RESULTS
The third party logistics company found by outsourcing the 3PL lost products project to RGIS, the following results were achieved:
- RGIS teams spent operational shifts locating misplaced parts
- The project allowed the 3PL to improve the inventory management accuracy quickly
- Warehouse operations did not need to shut down at any time during the project
- Root cause analysis allowed the supply chain to fix the put-away process
- Production schedules were able to stay on track during the project