Physical Inventory Solutions
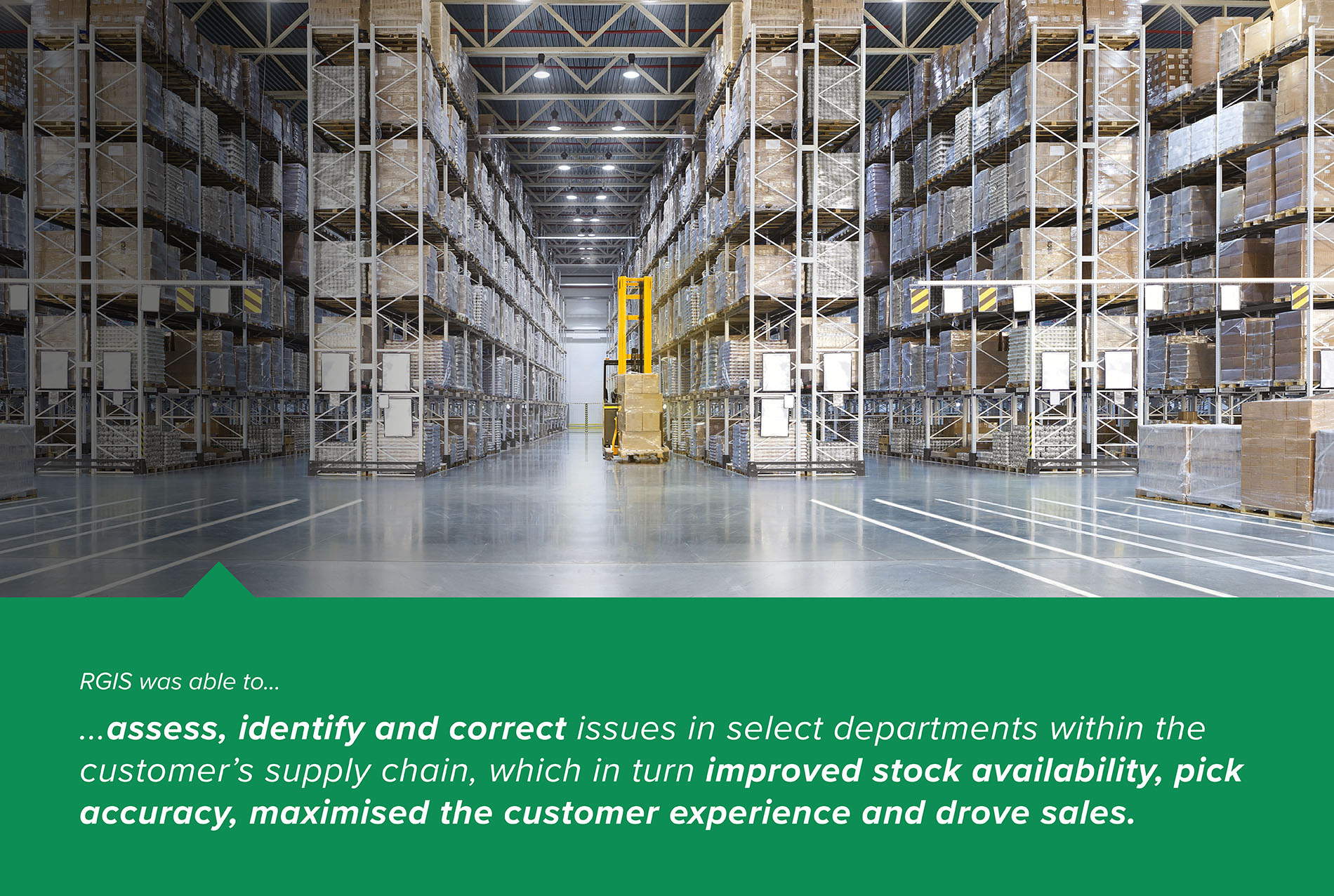
Tesco, a multi-national grocery retailer, enlisted the support of RGIS to assess, identify and correct issues in select departments within their supply chain. The aim of the project was to re-set stock records held in pick locations, which improves stock availability, pick accuracy, maximises customer experience and drives sales
REQUIREMENT
- Deliver a cost effective, targeted, inventory reset programme without compromising the distribution centre operation or customer service
- Improved inventory accuracy, driving improved pick availability and the right stock in supply chain at the right time
- Business insight in to product performance
- Identify losses and construct a plan to minimise in future
SOLUTION
RGIS worked collaboratively to produce a robust operational delivery plan, which required agreement and approval from multiple stakeholders. RGIS was able to:
- Provide dedicated Key Management and project support staff
- Assembling 80+ trained employees to conduct a wall-to-wall inventory correction programme across five separate sites
- Utilising real-time information, check, correct and update inventory records without affecting Live-Pick requirements
- Compare Physical Count vs. On-Hand Quantities, to identify and eliminate losses
- Identify how to increase the availability of fast-selling/fast-pick lines within the primary pick location, reducing need to pick from reserve locations, reducing down-time and improving DC efficiency
RESULTS
Through a proactive partnership approach, RGIS supported to achieve:
- Improved order fulfillment and pick efficiency, and corrected ‘out-of-stock’ issues
- Greater stock record accuracy, lower stock write-off, cleaner pick locations which resulted in reducing wastage and loss
- Real-time proof of delivery and site management
- Excellent operational accuracy, with > 99% Accuracy Control